At its core, CNC milling includes the elimination of material from a workpiece through a series of collaborated motions. The process begins with the design of a 3D model using computer-aided design (CAD) software. This model serves as the blueprint for the milling machine. As soon as the layout is finished, the operator uses computer-aided production (CAM) software program to equate the CAD model right into a set of guidelines that the CNC device can review, usually in the type of G-code. This code dictates the activities of the device's cutting devices, such as pin rotation and feed prices, making sure that every cut is replicable and exact.
Among the standout features of CNC milling is its flexibility. Unlike standard milling makers, which normally operate along one or two axes, CNC milling devices can operate on multiple axes simultaneously-- commonly 3, 4, or even five. This capability allows producers to accomplish a lot more complicated geometries than ever. A three-axis milling equipment can relocate along the Z, y, and x axes to develop a selection of forms, while a five-axis maker can turn the workpiece and tilt, allowing access to difficult angles and surfaces. This flexibility not just boosts layout opportunities yet additionally simplifies the manufacturing process, as it minimizes the requirement for several configurations and substantial hands-on interventions.
Explore cnc milling guide the transformative globe of CNC milling, a modern technology that incorporates accuracy and automation to create top notch elements effectively from various materials, and uncover its procedures, advantages, and key factors to consider for success in contemporary manufacturing.
The choice of devices is an additional critical facet of CNC milling. There is a wide range of cutting devices readily available, consisting of end mills, face mills, and sphere mills, each suited for various applications. End mills, for instance, are flexible tools that can be used for side and face cutting, while round mills are excellent for producing spherical corners and complex contours. The appropriate device choice can significantly impact the top quality of the completed product and the performance of the machining procedure. Additionally, correct device maintenance and problem surveillance play a considerable role in keeping ideal performance and extending device life.
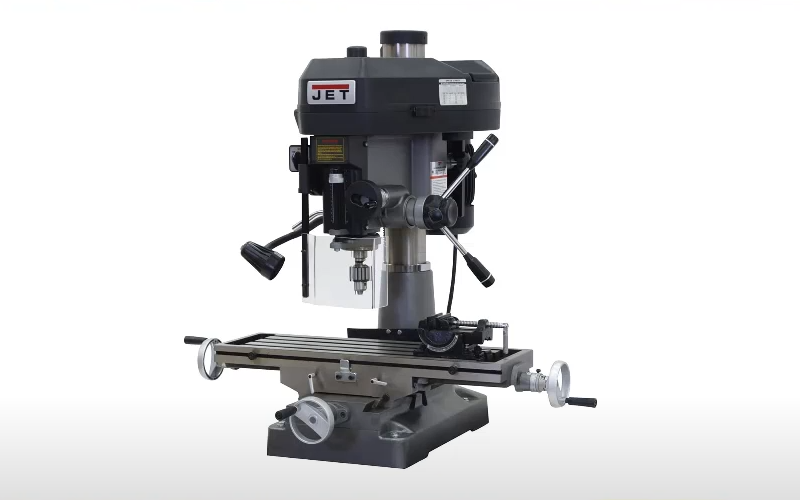
One essential variable to think about in CNC milling is worldly compatibility. Comprehending the buildings of the product, including its solidity, machinability, and thermal conductivity, allows drivers to optimize the milling procedure and achieve remarkable results while decreasing wear and tear on tools.
Beyond the technological factors like style, tooling, and products, there are additional considerations for maximizing CNC milling operations. Using advanced functions such as toolpath optimization strategies can streamline the milling procedure further, allowing much faster machining cycles and decreasing waste.
One of the significant benefits of CNC milling is the ability to automate recurring tasks, which lessens human error and boosts production uniformity. While traditional milling devices call for a skilled operator to look after the production process, CNC milling makers can run unattended, carrying out pre-programmed instructions with precision. This degree of automation not just boosts efficiency however likewise liberates skilled workers from mundane tasks, permitting them to concentrate on even more valuable activities such as quality control and process enhancement.
Regardless of its advantages, transitioning to CNC milling is not without obstacles. Initial financial investment can be considerable, with costs connected with acquiring CNC devices, software application, and knowledgeable employees training. Lots of services locate that the long-lasting cost savings connected with raised performance, lowered product waste, and improved item high quality exceed the preliminary prices. In addition, the schedule of renting alternatives and economical entry-level CNC milling makers has actually made it a lot more obtainable for tiny and mid-sized organizations to adopt this technology.
Training and ability advancement for personnel operating CNC milling equipments are additionally vital for taking full advantage of the roi. Operators need a solid understanding of both the CNC maker itself and the software application being utilized for programming and surveillance. Lots of makers find success by giving internal training programs or partnering with outside training organizations to outfit their groups with the required abilities and expertise.
In current years, technical advancements proceed to shape the area of CNC milling. As markets significantly transform to automation, integrating attributes such as synthetic knowledge (AI) and maker learning right into CNC devices can further enhance the precision and effectiveness of milling operations.
Advancements in software program are continuously tightening the gap in between design and production. Modern CAD/CAM systems now supply more instinctive interfaces and enhanced simulation capabilities, enabling drivers to imagine machining procedures before they are carried out. By spotting possible issues in the style stage, companies can solve design problems or maximize cutting approaches without incurring costly changes to physical materials.
In the context of CNC milling, sustainability is likewise obtaining significance as suppliers search for methods to lower their environmental influence. Implementing methods such as maximizing cutting specifications, making use of much more effective tooling, and reusing materials can add to an extra sustainable milling operation. In addition, technologies such as additive manufacturing are being discovered along with CNC milling, providing possibilities for hybrid manufacturing methods that additionally enhance sustainability by reducing waste.
Check out benchtop milling machine the transformative globe of CNC milling, a technology that integrates accuracy and automation to generate top quality elements successfully from various materials, and find its procedures, benefits, and key considerations for success in contemporary production.
In final thought, CNC milling represents an important asset in modern-day manufacturing, providing firms with the ability to create complicated and high-grade elements successfully. Comprehending CNC milling starts with a solid foundation in its processes, consisting of the interplay in between design, tooling, products, and software application. Inevitably, successful combination of CNC milling equipment, experienced labor force training, and wise automation paves the way for the future of manufacturing, where sustainability, efficiency, and top quality come to be the characteristics of operational excellence.